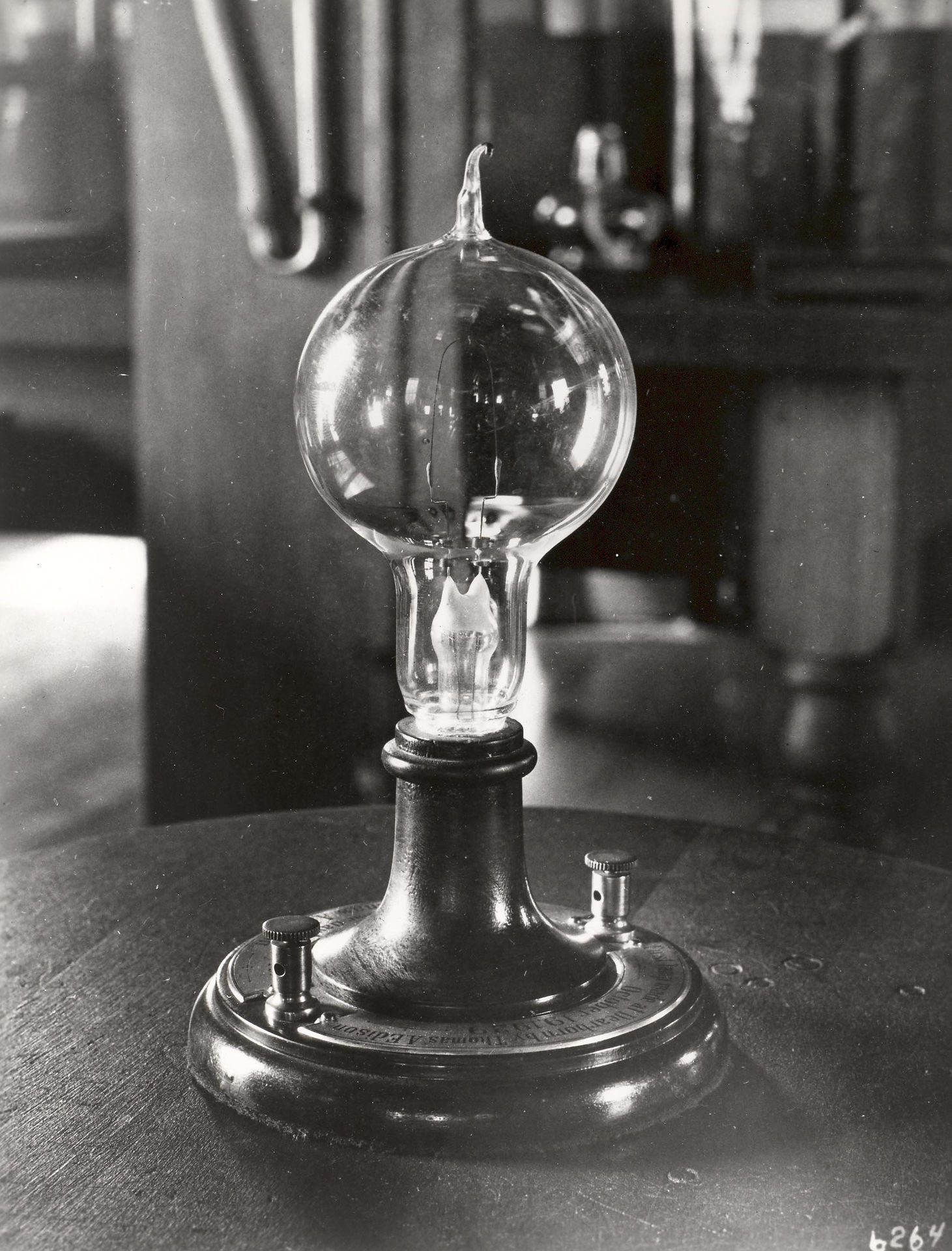
The History of Light Bulbs

"Genius is ninety-nine percent perspiration and one percent inspiration."
(Thomas Edison)
Edison Illuminating Company
The 1880s were a busy time for Thomas Edison. After being granted a patent for the light bulb in January 1880, Edison set out to develop a company that would deliver the electricity to power and light the cities of the world. That same year, Edison founded the Edison Illuminating Company—the first investor-owned electric utility—which later became the General Electric Corporation. In 1881, he left Menlo Park to establish facilities in several cities where electrical systems were being installed.
In 1882, the Pearl Street generating station provided 110 volts of electrical power to 59 customers in lower Manhattan. In 1884 Edison's wife, Mary, died, and in 1886, he married Mina Miller, 19 years his junior. In 1887, Edison built an industrial research laboratory in West Orange, New Jersey, which served as the primary research laboratory for the Edison lighting companies. He spent most of his time there, supervising the development of lighting technology and power systems. He also perfected the phonograph, and developed the motion picture camera and the alkaline storage battery.
Whatever the percentages, the concept is much the same for inventors today as for Edison. But circumstances have changed. Work is more often done in groups in large laboratories; scientific training is essential; equipment is complex and expensive. Here, we examine some of the differences and similarities between inventing Edison's lamp, and inventing six recent lighting devices.
Tungsten Halogen: Working in a Modern Industrial Laboratory
Edison assembled a team of talented assistants for his Menlo Park "invention factory." But he remained the guiding force behind the light bulb effort. From the initial experiments, through design of production equipment, to selling the lamp and its electrical infrastructure, Edison ran the show. Today, most lamps pass from one specialist or group of specialists to another as the original idea becomes a commercial product. Rarely does one individual oversee the entire process.
In 1950, at General Electric's Nela Park facility, Alton Foote led an effort to design a new heat lamp using a small tube of fused quartz rather than a large glass bulb. Foote found that quartz could withstand high heat, but the lamps blackened too quickly to be of use. Tungsten evaporated from the filament and settled on the inside wall of the tube, darkening the lamp.
Machinist turned inventor Elmer Fridrich, with the help of Emmett Wiley, placed some iodine in a quartz lamp and "Eureka! we put it on and instant success ... it was just beautiful." As seen in the image below, iodine cleared the tungsten atoms from the tube wall and returned them to the filament. Despite the initial success, follow-up experiments proved frustrating as some lamps worked and some that appeared identical failed.
In early 1954 chemist Edward Zubler was assigned to find out just what was happening inside the lamps, and in 1955 engineer Frederick Mosby transferred into the project to begin designing a marketable product. Fridrich and Wiley began playing a reduced role. After about three years of experiments Zubler and Mosby worked out the unique chemical and structural requirements of the lamp, some of which called for new procedures. For example, the tungsten filament wire had to be unusually pure, and this required the participation of engineers at GE's "wire plant."
A "pilot production" facility was set up to provide hand-made experimental lamps and by mid-1958 the team began to feel confident. As Mosby recalled, "Once management decided that we were ready to go beyond the piloting operation, we then called in our manufacturing people. They came in and looked at the lamp and decided what equipment we had to have in order to make this lamp at higher speeds, so prime responsibility went out of our hands at that time. We worked very closely with the manufacturing people, but it became their responsibility to get the equipment designed and made to put into our factories for expanded production."
In 1959, the tungsten halogen lamp was ready to emerge from the lab, bringing more new players into the process. Application engineers designed ways to use the lamps. Marketers began crafting sales pitches and researching needs that the new lamps might meet. This team approach has become typical of modern lamp invention.
By the 1950s, mercury vapor lamps were common and the subject of much research. In West Germany, Otto Neunhoeffer and Paul Schultz explored the use of halogens to combat electrode evaporation. Bernard Kühl and Horst Krense also tried halogens in a lamp and filed for a patent in August 1960. However, Osram had introduced an improved mercury lamp (designated H-33) without halides in 1959. The H- 33 lasted longer and was more efficient than older designs, and may have tempered commercial willingness to quickly introduce yet another improved mercury lamp.
At this same time, American physicist Gilbert Reiling was also experimenting with metal halides and mercury lamps. His work at General Electric's Research Laboratory involved a mix of theoretical studies and experimentation. Reiling was able to bring a high level of expertise to bear on the problem. "I had 11 years of college mathematics, from topography to matrices to tensor [states] - everything you could possibly mention in the field of mathematics, and you need that for the physics. I had made some thermodynamic calculations that showed that, with sodium iodide, the iodine was so powerful that sodium would not attack the quartz [envelope]. That's what so many people worried about, that these alkali metals were just going to chew up the envelope, but it turned out that the thermodynamics showed that it wouldn't, and it was that idea that really made this work."
Reiling's experiments with sodium and thallium (see lamps above) were promising enough that in June 1960 he reported to GE, "these lamps appear to have a higher luminous efficiency than the mercury lamp and the possibility for better color rendition." In September the lab's research director C. Guy Suits wrote to GE's Chairman Ralph Cordiner to tell him of the new lamp. Suits reported that, although the lamp produced white light "through a complex mechanism which our scientists are still studying in detail,... it now appears that little change will be required in manufacturing the new lamps other than simply adding a scientifically determined 'pinch' of the optimum compound." GE publicly announced the metal halide lamp in late 1962 and used it at the 1964 World's Fair.

"I knew what the lighting goals were,
everybody wanted more efficiency,
and they wanted white light,
and they wanted something economical."
Gilbert Reiling
Gilbert H. Reiling demonstrating
his metal halide lamp. 1962


Metal halide lamp
High Pressure Sodium: Studying Materials
Edison spent almost a year trying to develop a platinum filament for his lamp. The material would not burn up in air, but making it give light without melting proved difficult. Eventually Edison return to experimenting with carbon filaments, and he and his team baked hundreds of materials before settling on bamboo for their commercial product. The choice of materials is no less important today. Modern inventors simply have many more possibilities to chose from due to the great number of artificial materials unavailable a century ago.
Low-pressure sodium (LPS) lamps were developed in Europe early in the 1930s. Because sodium was very corrosive, LPS lamps needed special glass and very stable temperatures to operate. These factors led to complex glass-work, Dewar-type housings, and large fixtures. Research in the 1920s indicated that increasing the sodium's pressure would improve the lamps' poor color, but no practical material could be found that resisted sodium corrosion at the higher pressures.
After World War II, the GE Research Laboratory in Schenectady began a program to explore the properties of ceramics. Under the direction of chemist Joseph Burke, the program was designed to provide an understanding of ceramic processes. There was no particular product goal in mind, just fundamental research into a little known area.
In 1955 Robert Coble, a recent graduate from M.I.T., joined the team. A series of experiments ensued with polycrystalline aluminum oxide (PCA). Coble added magnesium to the mix, making a material Burke described as "more nearly transparent than had ever been hoped for. Actually, it was more nearly translucent. ... the material appears similar to a slightly frosted glass–but light transmission is from 90-95%."
Metallurgists and ceramicists worked on improving processing techniques needed to produce the new material (now called "Lucalox" for TranslucentAluminum Oxide) consistently, mainly by determining the manufacturing parameters. George Inman, a senior manager of GE's Nela Park lighting works in Cleveland heard of the PCA research during a trip to Schenectady in 1956 and directed engineer William Louden to begin assessing the possibilities of making a new lamp. In late 1957, Inman sent chemical engineer Nelson Grimm to Schenectady to learn about Lucalox and its manufacture. Grimm returned to Nela Park and established a "pilot-plant scale operation" that began providing tubes of the translucent material to Nela's lamp designers in 1958.
Lucalox tube
Physical chemist Kurt Schmidt began experimenting with different fill-gasses and in August 1959 filed for a patent on "Metal Vapor Lamps" that included sodium. Still, the lamps were not ready for sale. A difficult problem lay in sealing the ceramic tubes, since they could not be pinched shut like hot glass. Few sealing materials would stick to the new ceramic, and those that did needed to withstand the high operating temperatures and pressures of the lamp.
The task of designing the seals fell to Louden who later recalled, "The first seals that we made to Lucalox with metal were very short lived and we experimented for a long time with various methods of sealing. We got life out to 2000 hours, and at that point everybody began to recognize that we had something that might be commercially feasible." Niobium was chosen for the seal and made into a cap that expanded at nearly the same rate as aluminum oxide. However, niobium was a fairly exotic element, and new methods of working it had to be devised. Also, a material had to be found to serve as a "frit" (or caulking) between the niobium cap and the equally exotic ceramic tube.
In 1962 GE unveiled the new high-pressure sodium (HPS) lamp. A reporter covering the unveiling noted some bantering between Louden and Schmidt.
" 'He was destroying things as soon as they were made,' said the electrical engineer."
" 'He couldn't make them tough enough,' said the physicist."
Though reported as a joking exchange, the underlying situation was serious. The HPS lamp was not sold until 1965 and was redesigned in 1967. Continued materials research since that time has resulted in: clear ceramic tubes (Westinghouse & Corning, 1976); very high pressure lamps (Philips 1986); and "unsaturated lamps" (Philips, Sylvania 1993). In 1997, ceramic tubes were adapted to metal halide lamps.
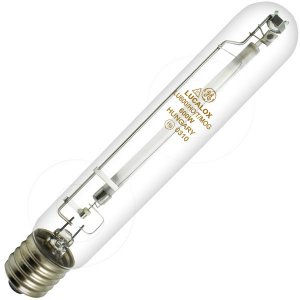
Fluorescent light bulb

The fluorescent light bulb has had a major development on the way we light up the world. Office buildings, schools and increasingly homes are lit by fluorescent lighting technology derived from General Electric’s 1938 invention. The fluorescent light bulb is increasingly seen as a replacement for less environmentally friendly alternatives, including the still used incandescent / tungsten rival. By the 1950s more light was produced in North America by fluorescent lights than by incandescent bulbs. The most important direct descendant of the 1938 fluorescent light bulb is the compact fluorescent light bulb, invented by General Electric’s Ed Hammer in response to the 1970s energy crisis.There is a debate to be had over whether fluorescent lights should entirely replace incandescent bulbs:
Drawbacks of Fluorescent Lighting
Fluorescent lighting has three main drawbacks. First, fluorescent lights are slow to start and often flicker. Second, many people prefer the light produced by incandescent lights, and find fluorescent lighting discomforting or unattractive. These problems, while not insurmountable, limit the sales growth of the fluorescent industry. The third problem is possible health effects. Critics of fluorescent lighting argue that the lighting can causeelectro-sensitivity and skin irritation, as well as damage to the environment from Mercury.
Advantages of Fluorescent Lighting
Advocates of fluorescent lighting counter with its high efficiency and ability to create significant energy savings. Fluorescent lights produce more illumination for less energy and they last longer. Advocates counter the claims about damage to the environment by arguing that energy savings more than offset any minimal damage done by mercury by reducing the risk of climate change. They also argue that negative health effects are unlikely and not proven. Regardless of whether one believes fluorescent lights should replace incandescent bulbs, co-exist with them, or not be used altogether, it is clear that the rise of fluorescent lighting has had a significant effect not just on how well the world is illuminated, but also what that world looks like.
The blue LED - modern LED Bulb

The 2014 Nobel Prize for Physics on Tuesday for inventing the new energy-efficient light source that led to the creation of modern LED light bulbs.
Shuji Nakamura, Isamu Akasaki and Hiroshi Amano won the prize for developing the blue light-emitting diode (LED) - the missing piece that now allows manufacturers to produce white-light lamps.
The arrival of such lamps has changed the way homes and workplaces are lit, offering a longer-lasting and more efficient alternative to the incandescent bulbs pioneered by Joseph Swan and Thomas Edison at the end of the 19th century.
"Red and green LEDs have been around for a long time but blue was really missing. Thanks to the blue LED we now can get white light sources which have very high energy efficiency and very long lifetime," Per Delsing, a member of the Royal Swedish Academy of Sciences, said.